
Higher yield materials between 60-85 KSI (with a low elongation percentage), a factor between 40-55% may be necessary. Using steels with yield strengths of 30-55 KSI with forming angles of around 90-degrees and a 1t – 5t inside bend radius, a “k” factor between 35-40% of the material thickness is most common. The use of restricted tolerance material will greatly improve part consistency but is rarely done, due to increased costs for raw materials.įIG #1: C-CHANNEL CROSS-SECTION WITH MATERIAL AND MILL SPECSįirst, consider the material to be formed. Unfortunately, many companies purchase their raw materials to the low side of the thickness range, to net more footage per ton, which leads to a lesser quality cross-section (poor dimensional and bend characteristics). This is done to eliminate interference between the male and female rolls when the material is passing through. When calculating strip widths and designing rolls, the maximum thickness within the gage range is generally used.

Various factors contribute to the bend allowance, such as material type and yield strength, profile characteristics, such as large radii or 180-degree bends, and roll design techniques.
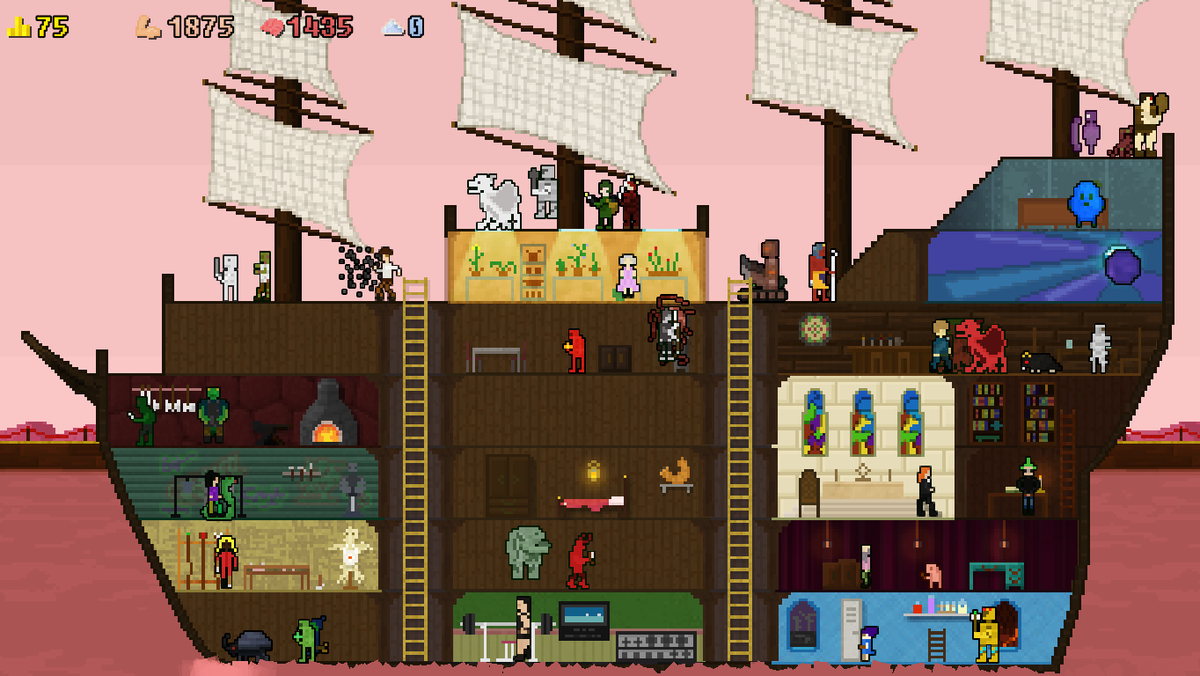
Using the proper “K” factor or “Bend Allowance” is the main item the designer must consider when calculating a strip width. Probably the most common problem associated with designing Roll Forming Tooling is predicting how a forming bend will react during the rolling process. Secondary processes, which can limit roll design options.ģ.0 CALCULATING THE ESTIMATED STRIP WIDTH.Pre-notching, pre-cut lengths, multiple gages.At the same time, other questions need to be answered, such as: Incorporate fixtures, guides, side rolls, and straightening devices where applicable.Īfter the cross-section has been finalized, and before the rolls can be designed, the proper number of passes and rolling mill must be determined.Layout and design the Roll Forming Tooling around the flower.Produce a Bend Progression or “Flower.”.Develop a cross-sectional drawing (with part, material, and mill specifications/tolerances).The basics are essential for the beginning designer.įor each new tooling requirement, the designer should use the following steps: With this in mind, we will only scratch the surface in this “basic” design guide. More commonly formed, or basic, shapes tend to have fewer variables and limitations, which in turn have higher levels of results that are both theoretical and repeatable. Past experiences, correctly applied, are still the key ingredients to the design and development of these applications.

Because the roll forming process has a seemingly limitless capacity to produce complex profiles with just as many variables, a high percentage of designs are one-of-a-kind. For a Roll Forming Tooling design, considering all the variables and applying “theory” whenever possible is vital in producing a good running product, with minimal start-up problems. In other words, a mixture of science and art is still very prevalent today in this industry. However, there are common design practices that must be understood and applied to the design process, coupled with a certain degree of “magic” (gained through previous experiences). Many roll designers have different approaches to both design and development (testing of tooling), and amazingly enough, there is more than one way to successfully form a profile.

In my experience, the ideas expressed in this report can be applied to many situations, but I will stop short of claiming that these are the only solutions. This paper is intended to provide “basic” Roll Forming Tooling design instruction and tips for the beginning or novice designer. Calculate Square & Rectangle Tube & Pipe.Tube and Pipe and Roll Forming Mill Evaluation
